EPA Screens 700 More Chemicals for Toxic Effects
by: Chemistry, 2010-11-30 22:46:03 UTC
Seven hundred chemicals are going through a federal chemical screening program, bringing the total number of chemicals to pass through the ToxCast tests to 1,000.
BAIC to Unleash Battery-replaceable EV in China in 2011
by: Tech-On! : tech news - straight from Asia., 2010-11-09 09:44:00 UTC
Beijing Automotive Industry Holding Co Ltd (BAIC) exhibited a battery-replaceable electric vehicle (EV) at the 25th World Battery, Hybrid and Fuel Cell Electric Vehicle Symposium and Exhibition (EVS25).
[FPDI/GD] AUO Exhibits Organic EL Panel for Lighting
by: Tech-On! : tech news - straight from Asia., 2010-11-12 09:14:00 UTC
AU Optronics Corp (AUO) exhibited a white organic EL panel for lighting at FPD International 2010/Green Device 2010, a trade show taking place in Chiba City, Japan.
Solar Cells Cut Generating Cost, Compete in Efficiency and Manufacturing Cost: Report from EU PVSEC
by: Tech-On! : tech news - straight from Asia., 2010-11-30 14:55:00 UTC
Photovoltaic cells-solar cells-are attracting increasing attention as the leader in renewable energy. Installation is accelerating in a host of locations, including homes, stores, plants and large-scale generation facilities, buoyed by national financial incentives and increasing public awareness of environmental issues. Compared to traditional generating methods, though, the generating cost is still too high.
Ecobuild
by: Sustainable Design News, 2010-11-29 14:40:01 UTC
 | Ecobuild is the world's biggest event for sustainable design, construction and the built environment and the UK's largest construction event of any kind.
In 2011 Ecobuild moves to its new home at the ExCeL exhibition and conference centre at the heart of the new Green Enterprise District in London's Docklands.
 |


How Manufacturing Affects Product Use Performance
by: Environmental Leader, 2010-11-29 17:59:12 UTC

Remember our discussion a while back about “buy-to-fly” ratio? This was referring to the amount of the materials that actually end up in the product as one metric of material utilization efficiency (July 2, 2010 posting). The variation in that ratio was impressive with some of our more sophisticated products having very low ratios (structural elements of aircraft, for example, due to the challenging requirements of shape and strength.)
Another consideration is impact, or resource utilization, from manufacturing the product versus using the product. That is, the use vs. manufacturing phase trade-off.
One of my research students, Teresa Zhang, had done an interesting analysis for a number of common products some time ago as part of her early work on her PhD in my lab. One of her charts is shown below and plots use phase resource intensity as a function of manufacturing phase resource intensity.
We see here that “things that don’t move or need power to operate” like bridges, furniture, etc., are dominantly manufacturing phase consumers of resources and, by extension, impact. Things that do “move and need power to operate” like automobiles, airplanes, etc., are use phase heavy. Interesting to note are the items that are close to the break-even 45 degree line. Personal computers overall, but not the chips in them, are a bit heavier in the manufacturing phase than use phase. Cell phones more heavy (but likely not if you include the embedded impact of the infrastructure needed to operate a cell phone network.) As usual, the details matter.
I was reminded of this during a presentation at a conference I attended recently in Germany during the presentation by a representative of the automaker VW in Germany. In the course of his slide show, he mentioned that, by their analysis, about 20% of the impact of a typical VW Golf A4 car came from manufacturing while 80% was due to the use phase. I had seen data on the GolfA3 (marketed from 1991-1999, also called the Polo) from some time ago and the comparison was similar. The figure below, from Volkswagen AG, and Harald Florin, PE Europe/IKP-University of Stuttgart, Germany (PE is the supplier of Gabi LCA software), shows the energy consumption during the manufacturing phase of the GolfA3 in Gj/auto.
Materials and part suppliers account for much of the embedded energy in the manufacturing phase. Machined components, such as the gear box and engine are a small percentage of the total (accounting for about 10% overall or about 25% with materials and parts from suppliers excluded).
If we look at the impact of the auto, including car production, fuel production and use phase, see below from the same source, we see that the fuel production and consumption in the use phase dominates all categories of emissions to air and water with the exception of dust generated by material production and casting of some components and painting of the vehicle and biological oxygen demand impacts on water.
More recent data I’ve seen from Volkswagen for the Golf A4 indicates that some improvements have been made – for example reduction of primary energy used in production, use and end of life due primarily to improved fuel consumption (a 20% improvement from 8.1 liter of fuel/100 km to 6.5 l/100 km for the gasoline engine).
In a posting on September 1st 2009 discussing the influence of precision manufacturing (and manufacturing in general) on environmental impacts I started out reviewing the basic impact equation (in terms of environmental damage, consumption, etc.) which is simply:
Impact = Population x (GDP/person) x (Impact/GDP)
I commented that population grows with time and most countries strive to improve GDP/capita since that drives living standards, etc. The rate of consumption or environmental impact per unit of GDP is the “rate of damage” done as a result of the technology driving the growth in GDP and is really the only “knob” we can adjust to reduce impact. I noted that engineers are most effective at changing technology that affects Impact/GDP. To the extent we can reduce that impact we are, effectively, greening the process.
So, if we look a bit closer at the VW numbers, does this make sense in terms of reducing the impact/GDP? If we focus only on manufacturing phase we may not be encouraged – specially if the predominant impact is in the use phase. Let me elaborate.
Let’s go back to our VW Golf example of 20% manufacturing phase impact versus 80% use phase impact. If we then think about the area I work in a lot, machining, and we assume about 20% of the manufacturing is machining or machining related, that gives us a potential for improvement of 20% of 20% or only 4% (and then if we get rid of all machining!). Let’s assume that some of the snappier technology for improving machining efficiency is employed, say some specialty tooling material that reduces machining power consumption, and that is worth another 20%. Now we are down to .8% (20% of 4%).
Hardly worth the effort, it would seem. Of course, if you are paying the electricity bill for the factory and this .8% technology wedge is added to a lot of others in machine operation it can add up to real savings. But, maybe still not impressive compared to use phase impacts. That is, over the full life cycle of the auto.
But, if we follow that logic we are leaving a lot of potential impact reduction from manufacturing on the table.
In the precision posting I referred to above, I mentioned that a major German auto manufacturer has been working to improve the “power density” of some of its diesel engines over the past years and has seen an improvement of almost a factor of 3 in power per unit of displacement. That means, for the same engine size (displacement) they have managed to squeeze three times as much power out. Coupled with advanced fuel injector systems operating at very high pressures (once thought absurd) they see enhanced performance in a small engine – increased fuel economy, improved acceleration (due to reduced mass), and reduced emissions.
The chart below, from Daimler, shows the improvement in power density as a function of time. The different colors indicate the increasing pressures in the fuel injector systems feeding fuel to the engine.
This is impressive and seems to keep growing without bound. Same size engine, better fuel efficiency and power generation.
How can this be?
Precision manufacturing! The posting on precision gives an example of how this could work for a Boeing aircraft based on tightened tolerances allowing increased structural performance by better control on dimensions – resulting in lower weight components. It is similar for the Daimler engine whose performance is tracked in the graph above. With better tolerances, better surface finishes, better control of orifice size and shape on the fuel injector nozzles (with diameters on the order of 60 microns), tighter control on cooling channels and fluid flow in the engine due to enhanced casting techniques, and on and on, the engine (still working on the same old Diesel principles) performs dramatically better.
The “dog leg” in the chart above corresponds to the introduction of high performance, precision, manufacturing to the power train in the automobile. Similar improvements can be see in the transmission as well.
That is how to reduce the impact per GDP.
Manufacturing dramatically increasing the efficiency of fuel utilization in the internal combustion engine. The small percentage of manufacturing phase improvement has a giant leverage effect on use phase impact. Since the principal element in use phase impact of the automobile the reduction in consumption (due to increased power density of the engine) hits both the fuel production impact as well as the fuel consumption impact. In the Golf A3 figure for emissions, 90% of the CO2 impact was due to use phase (81% from driving and 9 % from fuel production). A doubling of the fuel economy, by manufacturing induced engine efficiency improvements, by precision machining and processing will essentially halve that (same distance driven) – or account for, in the case of the Golf A3, a reduction of some 16 tons of CO2. And if, in the process of manufacturing enhancement, we save most of our 4% impact from machining, that’s .4 ton of CO2. So, for our .4 ton we get a return of 16 tons (a factor of 40!)
Now that’s a return you can’t beat.
The calculation may not be quite that simple, but we are seeing the same order of magnitude of leverage effect here. And some may argue that this improvement can’t be really counted as a greening effect of manufacturing. But, the motivation is enhanced performance which includes reduced impact. And it is due to manufacturing capability. I’ll take that.
That’s the true impact of greening manufacturing.
David Dornfeld is the Will C. Hall Family Chair in Engineering in Mechanical Engineering at University of California Berkeley. He leads the Laboratory for Manufacturing and Sustainability (LMAS), and he writes the Green Manufacturing blog.
Garden Fresh Air At Home
by: Yanko Design, 2010-11-30 09:19:42 UTC
Yanko Design is not new to air purifier concepts, however when it comes to the real thing, we have seen very few. To make up for the loss here is the O – Two Air Purifier, a small compact air cleaner that fits into the home environment seamlessly. It uses BioOx organic compounds to remove 99.9% of pollutants from the air you breathe and is silent as a lamb. It generates zero harmful waste, uses no filters, and uses less than 6 watts of energy while running!
Design-wise it looks sleek; aluminum vent accents wrap around a black plastic enclosure, topped by a large auto-dimming capacitive screen.
The unit currently is available for $399 here.
Designers: Laut Design, Studio Hagler & Montie Design
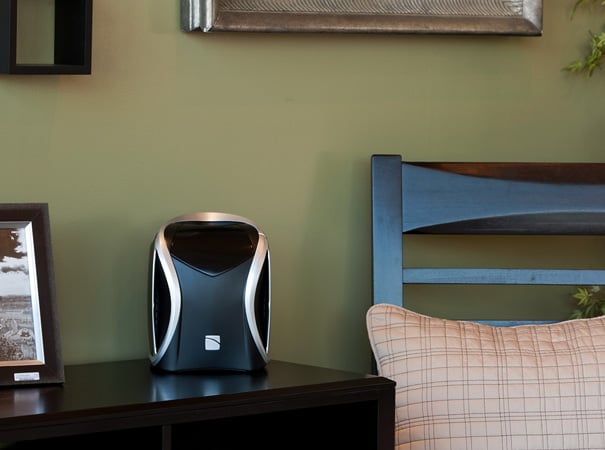
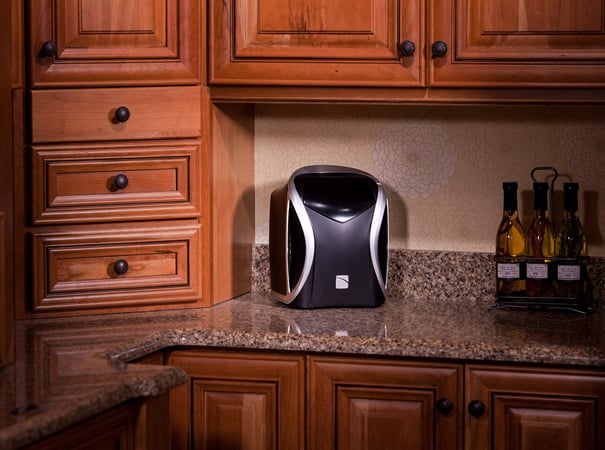
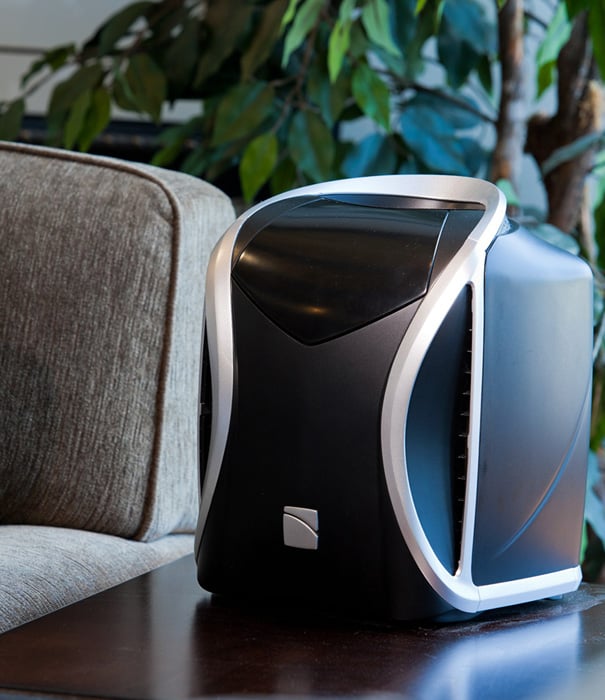
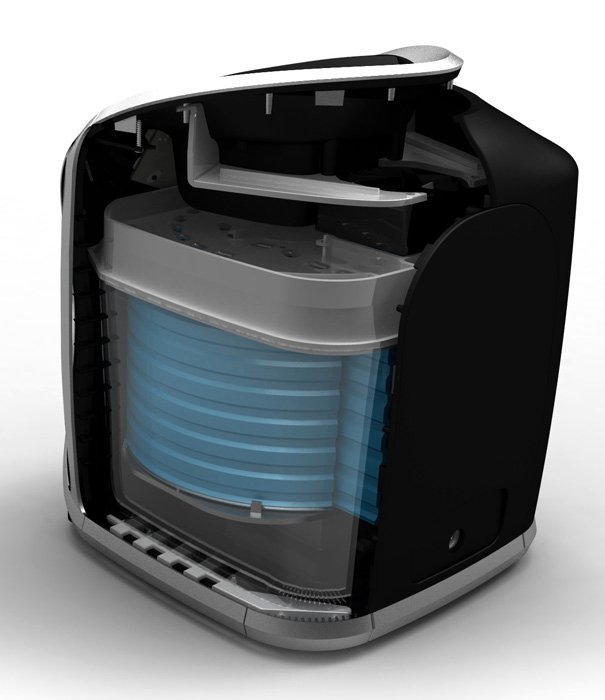
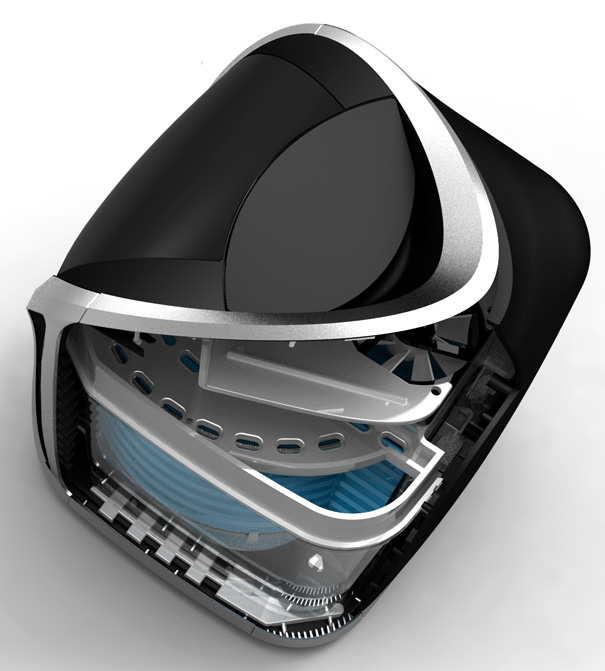
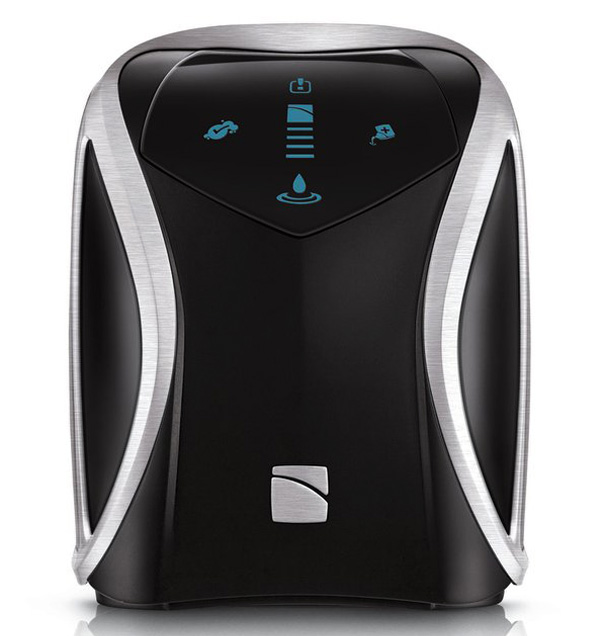
----------
Yanko Design
Timeless Designs - Explore wonderful concepts from around the world!
Yanko Design Store - We are about more than just concepts. See what's hot at the YD Store!
China Unveils Fuel Cell Light Rail Train
by: Eco Geek Latest, 2010-11-30 20:28:12 UTC

China has been making great strides in mass transit in the past year. They're building a
huge Asia-Europe rail network, rapidly
expanding their national high speed rail lines and have unveiled the
world's fastest high-speed train. The country has now revealed a fuel cell light rail locomotive for local, city-wide and suburban transportation.
The locomotive was developed by the China North Vehicle Yongji Electric Motor Corporation and the Southwest Jiaotong University. The train is powered by a permanent-magnet motor and hydrogen fuel cells that run a synchronous motor and frequency converter. This set up allows the train to produce and use power very efficiently while also cutting down on vibrations and noise.
The magnet motor out-performs traditional motors while reducing energy use by 10 - 20 percent.
via
Inhabitat
"Starbucks Calls Cup-to-Cup Recycling "Viable". I Call it Something Else.
by: TreeHugger Design, 2010-11-30 20:50:57 UTC

Starbucks has very proudly announced the completion of a pilot project where they have proven that paper cups can be recycled into new paper cups. They call it a breakthrough in their "goal of ensuring 100 percent of its cups are reusable or recyclable by 2015"
In a press release they say:
"This innovation represents an important milestone in our journey," said Jim Hanna, Starbucks director of Environmental Impact. "We still have a lot of work to do to reach our 2015 goal, but we're now in a much stronger position to build momentum across ... Read the full story on TreeHugger
"WindScanner" Uses Laser Beams to Measure Wind Conditions
by: fast company, 2010-11-30 18:36:05 UTC
Though it seems like something a Bond villain would dream up, the laser-enabled WindScanners might make the world a better place, by helping wind farms exploit energy more efficiently.
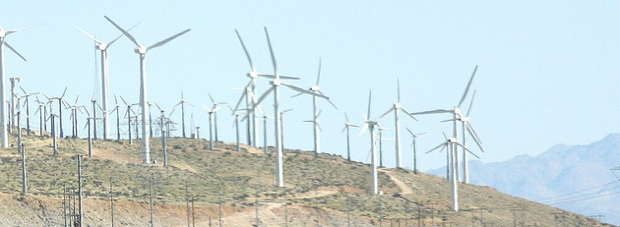
Three new energy research initiatives recently got a collective 1.2 billion Euros from the European Union. Among the beneficiaries is Risø DTU, at the Technical University of Denmark, whose laser-enabled "WindScanner" takes wind power measurement to a whole new level.
Shooting laser beams into the air seems weirdly aggressive in the context of gently spinning wind turbines, but the WindScanner turns out to be extremely helpful in mapping air conditions. One WindScanner consists of three white units called "Lidars" (after "Light Detection and Ranging"). Laser beams emitted from the Lidars are backscattered as they encounter whirling aerosols in the air, enabling the Lidars to infer the wind's motion and intensity.
Check out the animation below, courtesy of the Risø DTU site.
With three Lidars working together, the WindScanner can generate 3-D maps of wind conditions, helping wind farm operators to exploit wind energy with the highest efficiency. What previously would have taken a series of meteorological masts can now be determined with a suite of three Lidars, small enough to be packed into a van. So portable is the WindScanner that it doesn't necessarily need to be part of a permanent installation at a wind farm; it can even be dispatched to help troubleshoot wind turbines that are underperforming, as a sort of diagnostic tool determining whether the turbine or the weather is ultimately at fault.
[video_twistage 1]
[Images: Flickr user Kevin Dooley; Risø DTU]


Comments by our Users
Be the first to write a comment for this item.